PEB Building Supplier: Precise Engineering, Fast Delivery
Still confused about steel structure buildings?
A PEB building is a type of construction where components are prefabricated in a factory and then transported to the site for quick assembly.
Its design involves careful planning and calculations before the project kicks off, with all structural elements manufactured to precise specifications. This approach stands in clear contrast to traditional on-site construction.
In traditional building processes, much of the work—including material processing and structural erection—happens on-site. This not only makes the project vulnerable to external factors like weather but also extends the construction timeline significantly. In contrast, PEB components are produced in a standardized factory environment, allowing for stricter quality control. Once delivered to the site, skilled construction teams can assemble them rapidly, drastically reducing the overall construction period. For instance, an industrial workshop built using traditional methods might take six months or more to complete, while a PEB building could see its main structure finished in just a few weeks under favorable conditions.
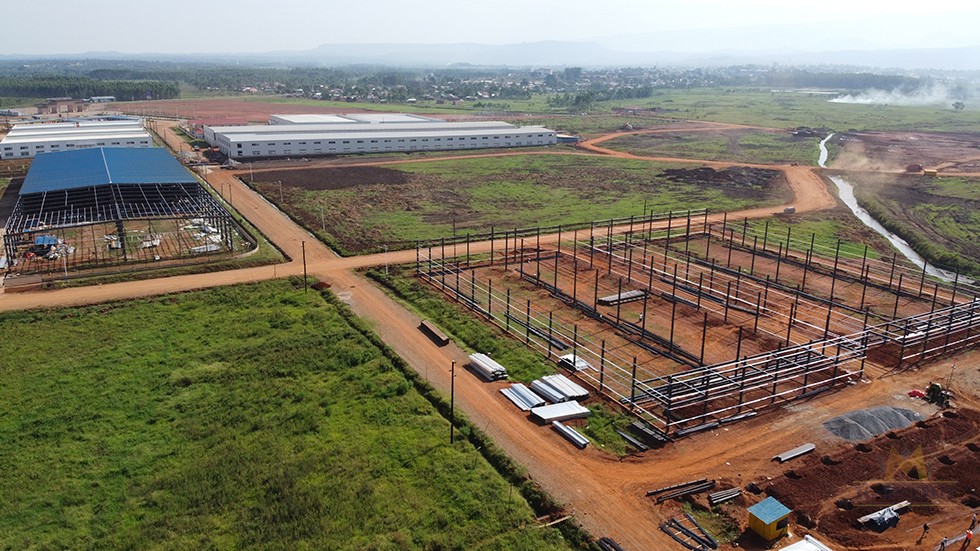
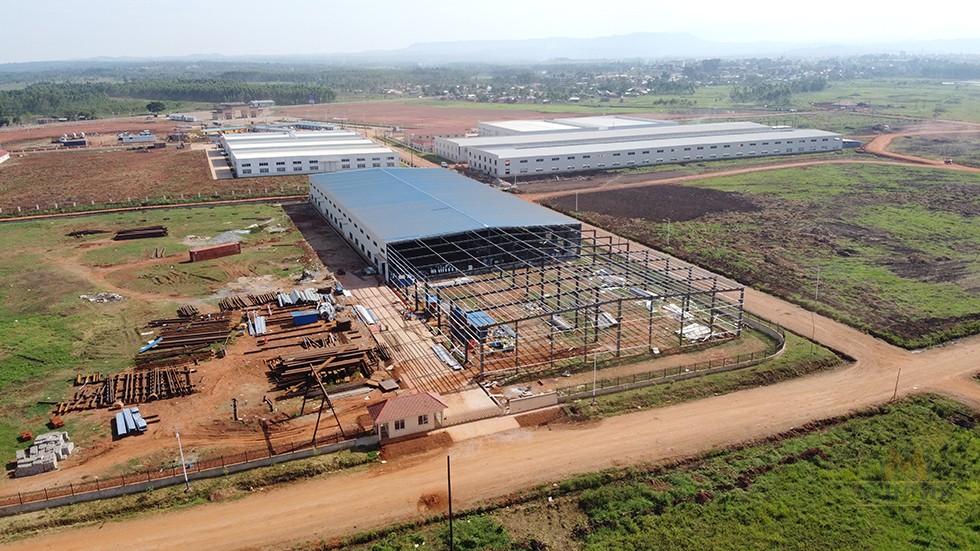
Choose the Right PEB Building to Address Your Quality Concerns and Cost Challenges
PEB buildings offer numerous advantages, with those in quality control and cost being particularly prominent. Since all structural components are manufactured in factories, factories can produce them in accordance with strict quality standards and advanced production technologies, and there are professional quality control engineers overseeing the entire process.
In contrast, when traditional buildings are constructed on-site, due to the complex and variable construction environment, it is more difficult to control quality. In terms of cost, PEB buildings, through optimized prefabricated design and production before leaving the factory, have reduced unnecessary material waste and labor costs. At the same time, the shorter construction period also better reduces the time cost of the project, such as reducing site rental fees and the usage duration of construction equipment. For example, for a warehouse factory that needs to be put into use quickly, using a PEB building can shorten the construction period and enable the project to be implemented more quickly.
One-Stop PEB Manufacturer with Comprehensive Steel Structure Construction Services
K-HOME (HENAN K-HOME STEEL STRUCTURE CO., LTD) was founded in 2007 as an international building company offering design, manufacturing, installation of metal structures, and building materials sales. With 35 technical experts and 20 professional construction teams, the company holds a Grade II General Construction Contractor license, providing global clients with end-to-end services from design and budgeting to production and installation.
For container houses, K-HOME uses precise CNC cutting machines and automatic bending machines to ensure structural accuracy within ±0.5mm, meeting strict temporary building standards. Equipped with large sandblasting lines and eco-friendly spray systems, their containers resist corrosion in hot, humid, or high-salt environments. Following ISO quality management, products are exported to the Middle East, Africa, Europe, and America for temporary housing, worksite camps, and commercial spaces. Leveraging extensive OEM prefabricated housing experience, K-HOME delivers customized designs for diverse needs, guaranteeing fast shipment and efficient installation.
With years of industry experience, excellent technical strength, and rich professional expertise, K-HOME has become a trusted benchmark enterprise in the industry.
Intelligent Prefab Steel Systems: Custom Solutions & Full-Project Support
We’ve independently developed intelligent design software tailored for PEB buildings. It quickly generates standardized solutions and precise quotations, slashing pre-project preparation time for your PEB projects. For clients with unique needs, our expert design team crafts optimized, custom PEB schemes, ensuring structural safety, cost efficiency, and a perfect fit for your specific pre-engineered building requirements.
In the PEB building sector, K-HOME stays focused on technological innovation and customer needs. Whether for industrial warehouses, commercial spaces, or public facilities, our pre-engineered building solutions deliver exceptional value, lowering overall costs while enhancing quality. Choose K-HOME, and you’ll gain not just top-tier PEB products but a reliable partner for end-to-end project support.
No matter what kind of steel structure building you need—whether it’s a large-span industrial workshop, a multi-functional commercial complex, or a specialized facility with unique layout requirements—our team can turn your specific ideas into tailored PEB solutions. We start by understanding your exact needs, from load-bearing demands to spatial planning, and then combine our intelligent design tools with expert engineering insights to create a custom pre-engineered building plan that fits perfectly. Every detail, from structural components to material selection, is optimized to match your project’s specifics, ensuring the final PEB building is not only safe and durable but also aligned with your budget and timeline.
Precision PEB Manufacturing Process: See How We Build Your Steel Structures
The manufacturing of prefabricated PEB (Pre-Engineered Building) steel structures follows a rigorous and standardized process to guarantee the precision and quality of each product:
Material Preparation & Collection:
Select steel and auxiliary materials that meet standards, have clear origins, and come with complete quality certificates. Strictly inspect the quality before warehousing, rejecting substandard items. Classify and store materials in designated areas to prevent environmental impact. Prepare the material collection area for smooth transportation and production. Ensure all equipment and machinery are ready for subsequent processes.
Press Forming:
Press metal panels and partitions into shape according to design specifications. Apply high pressure to transform steel billets into desired forms. Inspect dimensions and precision post-forming, comparing against technical drawings.
Shaped Steel:
After finalizing technical drawings, steel plates or sections are cut into specific dimensions and shapes—with the two main types of steel used being shaped steel (prefabricated steel), which consists of standard profiles like H-beams, U-channels, and C-sections requiring minimal trimming to meet design specifications, and composite steel, which is assembled from cut steel plates or coils tailored to project requirements—and high precision is achieved during cutting to ensure perfect fit during assembly, using modern cutting technologies such as laser cutting, plasma cutting, oxy-fuel cutting, circular/band sawing, and automatic slitting, followed by rechecking dimensions and removing defective parts before proceeding.
Component Welding:
Assemble steel parts into complete components using specialized automated welding systems for optimal precision and quality. Automated welding ensures uniform, durable, and aesthetically pleasing welds while minimizing human error. Thoroughly inspect welding quality, straightness, and angles before proceeding to the next stage.
Structural Adjustment:
After welding, the assembled components must be straightened using a dedicated straightening machine to eliminate warping, ensuring the flatness and standard angles of the components; subsequently, a special measuring ruler is used to check the flatness and verticality of the structure.
Connector Installation & Finishing Welding:
Install connectors (bolts, rivets, welds) to assemble structural components. Use proper tools and torque for bolt installation. Verify sub-component positioning and dimensions before welding.
Attach brackets, stiffeners, and ribs to the assembled structure using professional welding techniques to enhance load-bearing capacity and stability. Inspect weld strength, shape, penetration, and appearance post-welding, correcting any defects before moving on.
Surface Cleaning:
Clean the entire component surface with a shot blasting system to remove dirt, rust, and slag that could affect welding quality or paint adhesion. Ensure the surface is dry, clean, slightly rough, and flat.
Protective Coating Application:
Apply 1-2 coats of anti-rust primer as a base, followed by a specialized polyurethane topcoat meeting thickness specifications. The coating protects against environmental factors and extends service life.
Pre-Packaging & Shipping Inspection:
Conduct a final inspection of all components before packaging and storage. Protect the steel structure from scratches and impacts during transportation to the installation site.
- 1-Material Preparation
- 2-Steel Structure Forming
- 3-Structural Steel Straightening
- 4-Structural Steel Fitting
- 5-Structural Steel Welding
- 6-Structural Steel Abrasive Blasting
- 7-Structural Steel Weld Finishing
- 8-Structural Steel Coating
- 9-Structural Steel Inspection
- 10-Structural Steel Storage
Enclosure Structure of Steel Structure Buildings
Main Steel Component Structure
The main frame of a steel structure, like the “steel skeleton” of a building, consists of main steel, secondary steel, and purlins. The main steel adopts Q355B high-strength steel welded into H-beams; steel columns and girders, as core load-bearing components, support the main load of the building. Secondary steel, such as tie rods and bracing rods, is made of Q235B galvanized steel, which acts as “reinforcing links” to connect the main steel and enhance overall stability. Purlins are made of galvanized Z-section steel, fixing the outer materials of the roof and wall, respectively.
Enclosure Structure of Steel Structure Buildings
The main frame of a steel structure, like the “steel skeleton” of a building, consists of main steel, secondary steel, and purlins. The main steel adopts Q355B high-strength steel welded into H-beams; steel columns and girders, as core load-bearing components, support the main load of the building. Secondary steel, such as tie rods and bracing rods, is made of Q235B galvanized steel, which acts as “reinforcing links” to connect the main steel and enhance overall stability. Purlins are made of galvanized Z-section steel, fixing the outer materials of the roof and wall, respectively.
Efficient PEB Building Frame Shipping & Transportation Solutions
For PEB building components, our comprehensive containerization process ensures efficient and secure transportation from start to finish. Before loading, our professional technical team calculates the optimal cargo volume for each shipping container, maximizing space utilization while guaranteeing that all PEB components are included without any gaps or omissions.
Every package within the container is labeled with a detailed list of contents, and prior to shipment, we conduct rigorous inspections on quantity, dimensions, and product codes to confirm that customers receive all PEB building materials as ordered.
Once the PEB components are loaded, we enhance transportation stability by welding baffles to the tracks on both sides of the container, securing the cargo firmly in place to prevent movement and ensure safety throughout transit.
To streamline the unloading process, each packaged unit is equipped with a steel wire rope, allowing customers to pull entire packages out of the container directly upon receipt—an efficient method that saves time and reduces labor, typically enabling full unloading within just one hour.
Our proprietary containerization method, protected by a patent, allows us to load over 10 containers daily. This not only lowers packaging costs for our clients but also significantly cuts down on their unloading time and labor expenses, reinforcing our commitment to delivering efficient logistics solutions for PEB building projects.
FAQs About Prefabricated Steel Structure Buildings
Contact Us >>
Have questions or need help? Before we start, you should know that almost all prefab steel buildings are customized.
Our engineering team will design it according to local wind speed, rain load, length*width*height, and other additional options. Or, we could follow your drawings. Please tell me your requirement, and we will do the rest!
Use the form to reach out and we will be in touch with you as quickly as possible.