Quality Control Of Steel Structure Production
Gas cutting (cushion cutting or flame cutting) should preferably be CNC cutting, precision cutting, and semi-automatic cutting. When the above cutting is used unconditionally, manual cutting can be used, and auxiliary tools such as mold-making should be used. At the same time, 3-The machining allowance of 4mm is machined or smoothed with a grinding wheel.
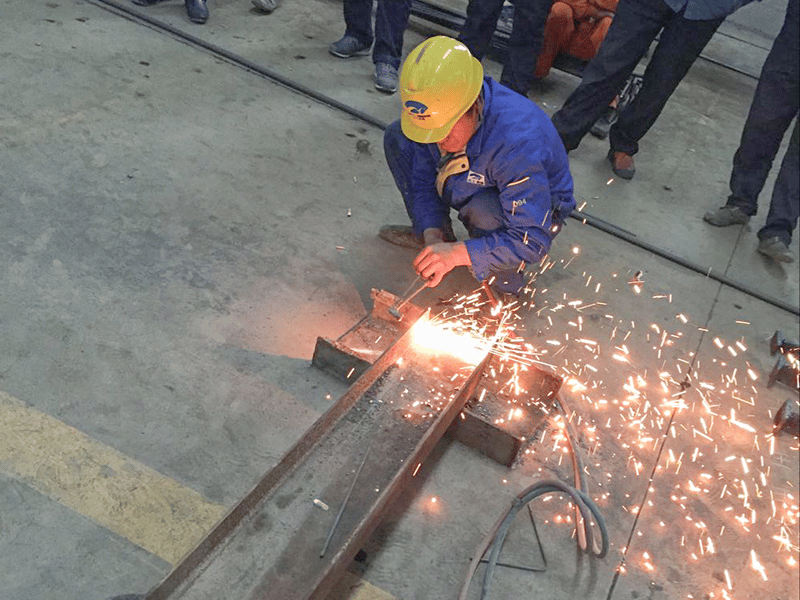
For strip-shaped steel plate parts, the long slits on both sides should be gas-cut at the same time to prevent the saber from being deformed. When unconditional gas welding is performed at the same time, segmented gas-cutting should be used, and 30-50mm is temporarily left between the two ends of the slit and between the segments. After the kerf is cooled, cut off 30-50mm everywhere.
Gas cutting should be carried out on a special platform, and there should be linear or point contact between the platform and the steel plate to be cut. All main components, unless otherwise specified in the design drawings, shall not be spliced with short materials.
All steels should be re-inspected according to the provisions of the corresponding specifications before use. If there is deformation, etc., the method should be straightened and corrected without damaging the steel. Connecting complex steel structures should be pre-assembled.
For the allowable deviation of welding, hole making and assembly of steel structural components, please refer to the “High Steel Regulations” and “Inspection Regulations”. The location of splicing nodes of large components shall be approved by the design unit.
Learn More About Influences the Price/Cost of Steel Building
Steel Structure Welding Construction Quality Control
Pre-weld preheating and post-weld heat treatment: For the welds that need to be pre-welded and post-weld heat treatment, the preheating temperature or post-heating temperature should be in accordance with the current relevant national standards or determined by the process tests.
The area is on both sides of the weld bead, and the width of each side should be more than 1.5 times the thickness of the weldment, and should not be less than 100mm; post-heat treatment should be carried out immediately after welding, and the holding time should be determined according to the thickness of the plate, 1h per 25mm plate thickness.
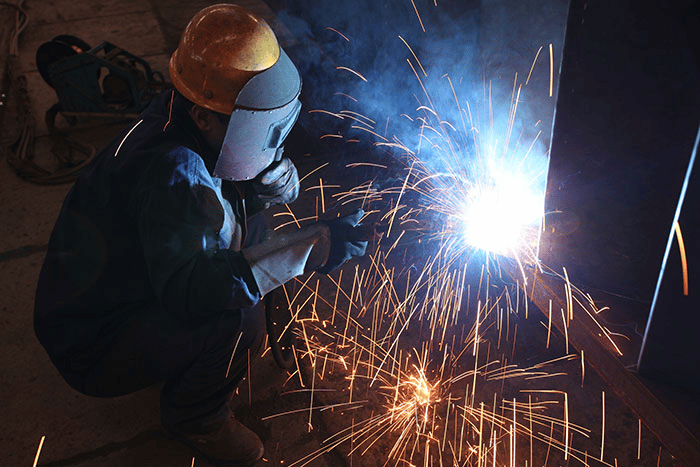
It is strictly forbidden to start the arc on the base metal outside the weld zone. The local area of arc starting in the groove shall be welded once, and no arc crater shall be left.
Multi-layer welds should be continuously welded, and each layer of welds should be cleaned in time after welding.
4The carbon structural steel should be cooled to the ambient temperature in the weld, and the low-alloy steel should be subjected to non-destructive inspection of the weld 24 hours after the completion of welding.
In the welding of thick plates and fillet joints with a thickness of more than 20mm, the construction unit (including the production and installation units should take all necessary measures to prevent laminar tearing in the thickness direction.
Moreover, when the plate thickness ≥ When the thickness is 30mm, in order to prevent layered tearing in the thickness direction, before welding, ultrasonic flaw detection shall be carried out in the area of 2 times the plate thickness plus 30mm on both sides of the centerline of the base metal weld. There shall be no cracks, interlayers and Defects such as delamination exist.
When the village backing plate is used for welding, in addition to the gap size at the root of the welding groove, which must meet the design requirements, the backing plate and the weldment should be closely attached, so that the welding flow can dissolve into the backing plate, and meet the following requirements:
- The technical requirements of the backing plate should be the same as the welding material.
- The pretreatment method of the backing plate should be the same as that of the welded components.
- After the welding is completed, the backing plate is removed by cutting. The original part of the connection between the component and the backing plate should be smoothed and checked for any cracks.
When welding on the embedded parts, measures such as thin electrodes, low current, layering, and interval welding should be used to control the temperature of the entire embedded part to avoid burns and coagulation.
When welding around the three sides and around the fillet, the corners must be continuously welded. Steel structural members shall not be welded under stress. Welds should avoid overlapping each other as much as possible.
Steel Structure Installation Engineering Construction Quality Control
- When hoisting the section steel column, use the two-point hoisting method. After the hoisting is in place and fixed, temporary support is provided to prevent it from being tilted by wind or other external forces.
- The steel structure should have a product quality certificate when it enters the site, and its sub-projects such as welding connection, fastener connection, and steel component production should be qualified.
- Check the stability of component hoisting, select hoisting machinery reasonably, and determine an economical and feasible hoisting plan.
- The steel structure should meet the design requirements and specifications. The deformation of the steel structure and the peeling of the coating caused by transportation, stacking, hoisting, etc. must be corrected and repaired.
- For the installation of multi-layer or high-rise frame members, after the hoisting of each layer is completed, it should be corrected according to the intermediate acceptance records and measurement data, and the manufacturer should be notified to adjust the length of the members if necessary.
- For the nodes that are required to be tight in the design, the two planes in contact must be 70% close to each other and checked with a 0.3mm feeler gauge. The maximum gap between the edges shall not be greater than 0.8mm.
- The position of the horn should ensure the rigidity of the bottom of the column, and the arrangement of the horn should allow the column or base to bear additional loads.
- The positioning axis of each column should be led directly from the ground control line, not from the axis of the lower column; the floor elevation of the structure should be controlled according to the relative elevation or design elevation.
- After the space stiffness unit is formed, the gap between the column bottom plate and the foundation surface should be replaced by fine stone concrete and grouting material in time.
- When the steel structure is transported, stacked and installed, the stability of the structure should be ensured, and the structure should not be permanently deformed.
- Between the steel components connected by high-strength bolts, reaming is not allowed at will, and gas-cutting reaming is strictly prohibited. 12. For the installation accuracy and allowable error of components, please refer to “High Steel Regulations”, “Steel Regulations” and “Inspection Regulations”.
- Pre-embedded bolts: During the pouring process, it is necessary to ensure that the foundation bolts remain in place. At all stages of construction, measures must be taken to protect bolts, threads and nuts from damage, corrosion and contamination. The bolt guards buried in the foundation should be kept clean and free of debris.
- Grouting: The grouting of the bottom plate of the column base must be carried out after the structure has passed the alignment, level and verticality test, has sufficient support, and is accurately and firmly connected with the permanent connecting member. The space under the base plate must be removed and cleaned before grouting. Commercial grout shall be prepared, mixed and grouted according to the manufacturer’s instructions. Tests should be carried out if necessary.
- When installing the profiled steel column, control the flatness and compactness of the column foot, tighten the stud bolts, and master the verticality of the profiled steel column.
Further Reading: Steel Structure Installation & Design
Steel Structure Anti-Corrosion Construction Quality Control:
Before the steel structure is painted, the burrs, rust, oxide scale, oil stains and attachments on the surface of the components must be completely removed, and the rust should be thoroughly removed by sandblasting, shot blasting, etc. On-site paint and rust removal can be done by electric motors. , Pneumatic rust removal tool thoroughly removes rust, after the steel surface rust removal is qualified, it should be painted within the required time limit.
For the parts that have been anti-rust primer, but there is damage, rust, peeling, etc., and parts that have not been anti-rust primer, they should be treated with paint touch-up. The specific requirements are: use epoxy zinc-rich primer as the repair anti-rust primer, and then according to the location, make the sealer, midway paint, and topcoat in order.
After the bolts connected on-site are screwed, the anti-rust paint should be applied according to the design requirements. For the bolts used in the open air or in the corrosive medium environment, in addition to applying anti-rust paint, the joints of the connecting plates should be sealed with ointment or putty in time.
Construction Quality Control Of Steel-Concrete Structure:
In order to solve the spatial contradiction between the profiled steel and the steel bars at the beam and column joints in the profiled steel-concrete frame, so as to realize the continuity and penetration of the main bars in the column from bottom to top and ensure its integrity, it is necessary to process the profiled steel beams and columns before processing.
Carry out the detailed design of the perforation position of the steel bar: In addition, in order to use the pull bolt when the formwork is supported, the detailed design of the position of the pull bolt eye on the steel column must be carried out.
Before the installation of the steel structure, the positioning axis of the building, the axis of the foundation and the position and elevation of the anchor bolts should be checked, and the foundation should be tested and the handover and acceptance procedures should be carried out.
The strength of the foundation concrete must meet the design requirements before installation; the reference point of the foundation axis mark and elevation must be accurate and complete; the installation of the profiled steel column: control the elevation, control the verticality, control the position, the position of the anchor bolt and the supporting surface must be accurate.
The steel plate backing plate used in the installation of the profiled steel column should be set under the bottom plate of the column foot close to the anchor bolt, and two groups of backing plates should be arranged on the side of each stud bolt. The contact between the backing plate and the base surface and the bottom surface of the column should be flat and tight. Before grouting the bottom plate of the column base, the backing plate should be welded and fixed.
The main reinforcement of the reinforced steel column should be inserted in strict accordance with the detailed design results of the position of the main reinforcement. It must be ensured that the position of the main reinforcement passing through the flange plate of the profiled steel beam is accurate, and the verticality of this part of the reinforcement is required during the entire construction process of the column.
When installing the main reinforcement through the profiled steel beam or the steel support corbel flange plate, first pass the reinforcement to be connected through the reinforcement hole from bottom to top, and then use a special sleeve to connect with the lower reinforcement.
The stirrups at the joints of the profiled steel-concrete frame can only be processed into open sleeves due to the influence of the profiled steel beams and the steel support corbel webs. Factory pre-soldered) welding.
During the processing of the anchoring steel plate at the top of the column, it is necessary to reserve reinforcement holes according to the results of the deepening design of the main reinforcement arrangement. The weld should be filled with the gap between the reserved hole and the reinforcement, and the top of the weld should be flush with the top surface of the anchor plate;
Carefully consider the length of raw materials, make reasonable ingredients, and control the number of steel bar joints in the same section to meet the requirements of the specification.
The position of steel bar joints, the spacing of stirrups, and the angle of stirrup hooks must meet the requirements of construction specifications and design, and concealed acceptance must be done.
Before the column is supported, the wire should be popped out on the bottom surface, and the position of the column should be centered, and the position of the reinforcement of the column should be corrected.
Concrete pouring Due to the dense reinforcement around the section steel and the influence of the section steel beam on the top of the column, it is difficult to pour with ordinary concrete. The selection of self-compacting concrete with self-leveling and self-compacting properties can well ensure the construction quality.
Concrete pouring speed cannot be If it is too fast, the ash height should be controlled at about 0.5m each time, and the time interval between two times of ash should be controlled at about 15 minutes.
When pouring concrete, use a rubber hammer to strike the outside of the formwork, especially the four corners of the column, so as to check whether the concrete is poured tightly, and it is helpful to eliminate the pores inside the concrete.
Contact Us >>
Have questions or need help? Before we start, you should know that almost all prefab steel buildings are customized.
Our engineering team will design it according to local wind speed, rain load, length*width*height, and other additional options. Or, we could follow your drawings. Please tell me your requirement, and we will do the rest!
Use the form to reach out and we will be in touch with you as quickly as possible.
About Author: K-HOME
K-home Steel Structure Co., Ltd covers an area of 120,000 square meters. We are engaged in the design, project budget, fabrication, and installation of PEB steel structures and sandwich panels with second-grade general contracting qualifications. Our products cover light steel structures, PEB buildings, low-cost prefab houses, container houses, C/Z steel, various models of color steel plate, PU sandwich panels, eps sandwich panels, rock wool sandwich panels, cold room panels, purification plates, and other construction materials.