Prefabricated buildings that are energy-saving and environmentally friendly are one of the buildings that are vigorously promoted by the country. In prefabricated buildings, there are wood-structured houses and steel-structured houses with different characteristics. Let’s take a look at the difference between these two prefabricated houses.
Greater structural strength and integrity
Steel structural members are manufactured to very strict standards and specifications. In pre-engineered metal buildings, there are no seconds or off-spec materials. Every component in a metal building meets stringent industry standards for strength and is designed for its intended use in that particular metal building.
This is important when we discuss the bespoke requirements of each specific job: each component in a steel building is designed and fabricated to meet the stringent loading standards of each individual structure, ensuring that each steel building can handle its All load requirements for a specific site at the location. Because of this, properly designed and assembled metal buildings have withstood hurricanes, tornadoes, and extreme conditions worldwide.
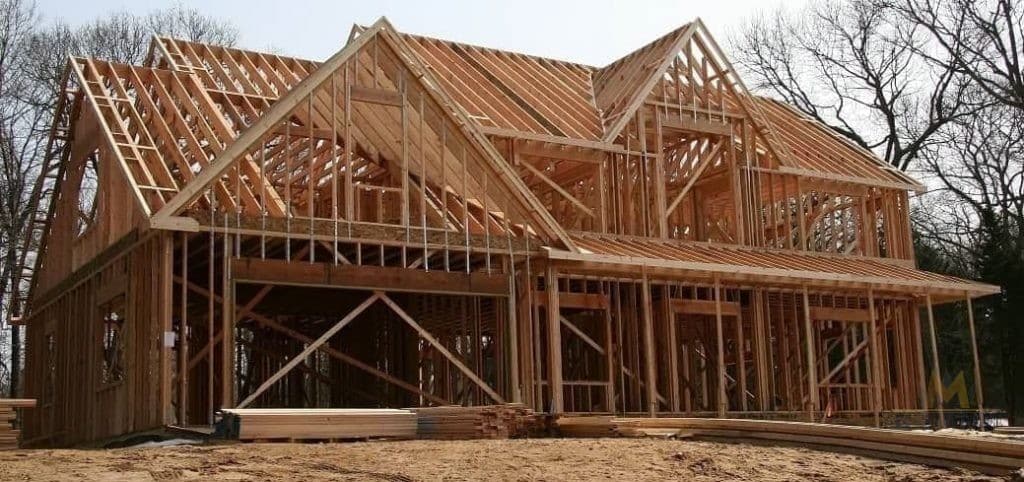
Faster, easier and cheaper to build
Each prefabricated steel building component is designed and manufactured specifically for your building. Each component is designed and manufactured to perfectly match the others. Each piece is labeled and easily identifiable, and each piece is cross-referenced on the assembly drawing. This means your steel building – big or small – will arrive as a perfect kit, each piece will fit together precisely.
Because each component is handled in detail and manufactured specifically for each specific structure, building a building is quick and easy. In turn, steel buildings require less labor because they can be assembled quickly and easily. There is virtually no waste and virtually no cutting, sewing, or welding on site.
Learn More About Influences the Price/Cost of Steel Building
Wooden buildings take significantly longer to build than pre-engineered packages simply because all components are sourced and sourced individually. There are more measurements, more cuts, and more margins for error, all of which take a lot of time. It also generates more waste because once the components arrive at the job site, they have to fit.
A final consideration is that the price of lumber is constantly fluctuating. Frequent lumber shortages have pushed up lumber costs. This encourages the use of “green” wood in building projects, which can lead to warping, cracking, and splitting. These cracks in wood elements can affect tightness, thereby reducing the energy efficiency and structural integrity of the final structure.
Safer – throughout the life of the building
Steel parts will not age or degrade over time like wood. Steel does not rot. Steel will remain rigid throughout the life of the building. This structural strength means less stress on fasteners and components; this, in turn, provides safer construction for years to come.
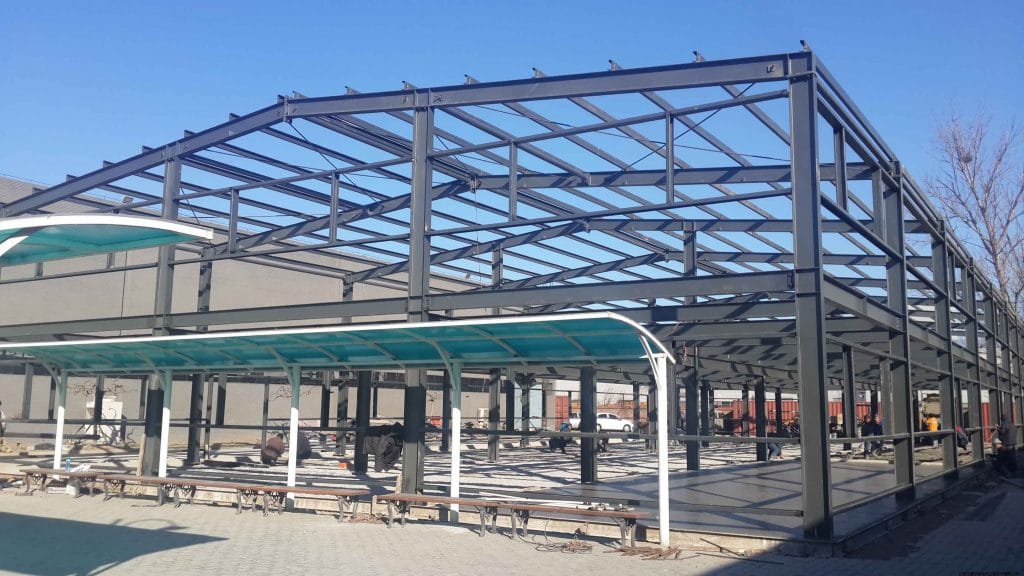
Alternatively, owners of timber structures need to invest in ongoing maintenance. With wood, as long as there is moisture near the bottom, there is a chance of rot. A recession can lead to structural insecurity and increase the risk of collapse. To address the natural properties of wood, most wood posts are pressure treated, but the process can be toxic to livestock or other animals if ingested.
Importantly, wood carries the fear of fire loss. The real peace of mind that comes with choosing steel buildings is the safety of your people, livestock, and property; because steel is non-combustible.
Greater design flexibility
Since steel is much stronger than wood, it allows for greater design flexibility. You can often span the entire width of the building without the need for internal pillars, and you can set the pillars farther out on the side walls. The result is a more open building with less weight and higher structural integrity.
When wood trusses are used to complete open spaces, they must be layered and connected in several places. This increases the cost exponentially. This is why timber structures often involve several internal columns and beams that limit the usable, clear span area and thus reduce workspace.
Reduce maintenance costs
Steel parts will not warp, crack, twist, expand, shrink or rot like wood. Steel members will not have to be replaced or repaired, and will remain long after the wood-frame building is gone.
Contrary to the lightweight 28 or 29 material used in most wood-pole barns, prefab metal buildings use at least 26-gauge plank for roofing and siding. Fasteners in steel buildings are also of higher quality and do not need to be replaced like in typical wooden pole buildings.
Over time, the light metal panels on most wood pole buildings will need to be replaced, and the wood slides will retain moisture on the light metal panels, causing premature rusting of the metal panels and fasteners. In this case, the fastener loses grip and the sheet becomes loose and needs to be repaired or replaced. In addition, regular high maintenance is required to ward off rodents and burrowing insects and to limit the amount of rot and mold in wood structures.
None of these are issues when you choose prefab metal buildings. Steel structures are virtually maintenance-free
Longer economic life – more durable and worry-free
Steel structures do not wear out over time as wood structures do. Unless something catastrophic happens, your steel building will last a lifetime. Wooden buildings have an economic life of 15-20 years and require a lot of maintenance in the process. After about 7 to 10 years, the wood siding and roof will have to be replaced. If a non-metal roof is used, it will also need to be replaced at some point. As wood structures age, wood components naturally dry out, leading to shrinkage, warping, expansion, and cracking. Preventing wood structural elements from drying out is necessary to keep the structure safe, but requires ongoing maintenance and close attention.
In contrast, pre-engineered metal buildings require little maintenance and provide decades of worry-free service.
Lay a solid foundation
The first objection that some people have raised against steel buildings is that it requires concrete foundations and floors, which add significantly to the initial cost of the project. A metal building does not always require a full slab, although it does require concrete piers at each column location to provide proper structural stability and meet design load requirements. The required piers provide load-bearing capacity and a connection above the ground so that the columns do not get damp and rot. Foundation requirements depend on the building application and site location. The local licensing office will assist in determining which foundations are deemed suitable for a particular building and city.
While foundations do add to the initial cost of a metal building system, the benefits over the life of the building are enormous and outweigh the initial cost.
The steel structure is more environmentally friendly
Steel is 100% recyclable and is the only recycled material that does not lose strength when recycled. Remember that there is also no waste when fabricating and constructing steel buildings, as there is no need for a lot of cutting on-site, and all the cuttings from the factory can be recycled.
Compared to wasteful and non-recyclable wooden buildings, metal buildings are the best option for protecting the environment.
Steel buildings can actually save you money – year after year
In addition to ongoing savings related to maintenance, the steel building has a fire rating of “A”. In contrast, wood-frame buildings have a fire rating of “C”. Generally, this means that wood structures are more likely to burn. Many customers don’t realize that this incombustibility factor can save significant insurance premiums over the life of their prefabricated steel buildings.
Further Reading: Steel Structure Installation & Design
Contact Us >>
Have questions or need help? Before we start, you should know that almost all prefab steel buildings are customized.
Our engineering team will design it according to local wind speed, rain load, length*width*height, and other additional options. Or, we could follow your drawings. Please tell me your requirement, and we will do the rest!
Use the form to reach out and we will be in touch with you as quickly as possible.
About Author: K-HOME
K-home Steel Structure Co., Ltd covers an area of 120,000 square meters. We are engaged in the design, project budget, fabrication, and installation of PEB steel structures and sandwich panels with second-grade general contracting qualifications. Our products cover light steel structures, PEB buildings, low-cost prefab houses, container houses, C/Z steel, various models of color steel plate, PU sandwich panels, eps sandwich panels, rock wool sandwich panels, cold room panels, purification plates, and other construction materials.