There are many welding methods in steel processing, but arc welding is mainly used. Because arc welding equipment is simple, easy for workers to operate, and the quality of the weld is reliable, there are many advantages.
Arc welding can be divided into manual arc welding, automatic or semi-automatic submerged arc welding and gas-shielded welding according to the degree of automation of operation and the type of material used to protect the molten metal during welding.
Then the following are the welding methods of these steel structures.
Further Reading: Welded Splice Joint in Steel Structure
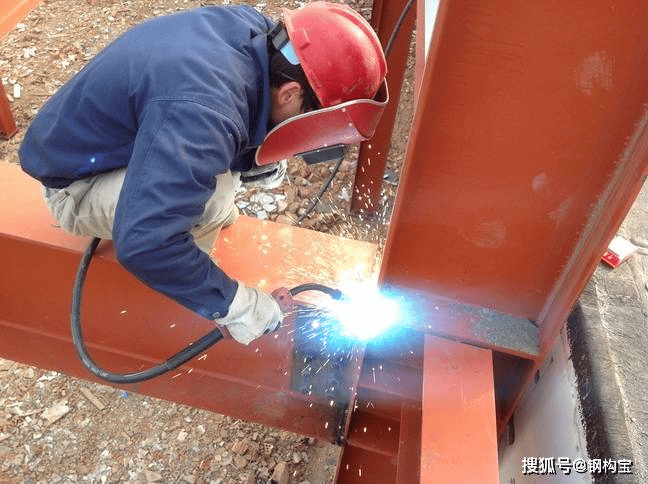
3 Types of Arc Welding
1. Manual Arc Welding
The method of relying on the heat of the arc is called arc welding. Manual arc welding is a kind of arc welding with manual welding rod, which is commonly used in the welding of steel structures.
The weldment and the electrode are two electrodes that generate an arc, the arc generates a lot of heat, the weldment and the melted electrode, the electrode end melts to form a droplet, the transition to the fusion of the base metal of the melted weldment, the formation of a pool and a series of complex physical-metallurgical reactions. As the arc moves, the liquid molten pool gradually cools and crystallizes to form a weld.
Under the action of high temperature, cold in the electrode coating on the steel reinforced molten slag, covering the surface of the molten pool of metal, it can not only protect the high temperature of the molten pool of metal and the harmful reaction of oxygen and nitrogen in the air, and can also participate in the molten pool chemical reaction and seeping alloy, etc., in the cooling and solidification of metal surface, form protective slag shell.
2. Automatic or semi-automatic submerged arc welding
Automatic submerged arc welding is superior to manual welding because of the concentration of arc heat, so it has a large penetration depth, uniform weld quality, fewer internal defects, good plasticity and impact toughness. The quality of semi-automatic submerged arc welding is between automatic submerged arc welding and manual welding.
In addition, automatic or semi-automatic submerged arc welding has high welding speed, high production efficiency, low cost and good working conditions. However, their application is also limited by its own conditions, because the welder must move along the guide rail of the weld, so there must be certain operating conditions.
3. Gas-shielded welding
Also known as fusion gas arc welding, CO2 or inert gas is used to create a local protective layer around the arc to prevent the invasion of harmful gases and ensure the stability of the welding process.
All-position welding, good quality, fast melting speed, high efficiency, energy saving, no need to remove welding slag after welding, but it is worth noting that attention should be paid to avoid wind when welding.
Welding Materials
Welding materials include electrodes, wire, metal powder, flux, gas, etc.
welding rod
A strip of metal that fills the joint of a welder during gas or electric welding. The electrode is usually made of the same material as the workpiece. The electrode is a melting electrode for electrode arc welding with coating, which is composed of coating and welding core.
welding wire
The wire is a wire welding material used either as filler metal or as an electrical conductor. In gas welding and tungsten gas-shielded arc welding, the welding wire is used as filler metal; In submerged arc welding, esG welding and another GAS-shielded arc welding, the welding wire is both the filler metal and the conductive electrode. The surface of the welding wire is not coated with anti-oxidation flux.
Metal powder
Metal powder refers to the metal particle group whose size is less than 1mm. Single metal powder, alloy powder and some refractory compound powder with metal properties is the main raw material of powder metallurgy.
Flux
Flux, also called brazing agent, has a wide definition, including molten salt, organic matter, active gas, metal steam, etc., that is, in addition to the base metal and solder, generally refers to the third kind of material used to reduce the interface tension between the base metal and solder.
Gas
Gas is one of the four basic states of matter (the other three are solid, liquid and plasma). Gases can be composed of a single atom (e.g., noble gases), elemental molecules of one element (e.g., oxygen), compound molecules of many elements (e.g., carbon dioxide), and so on.
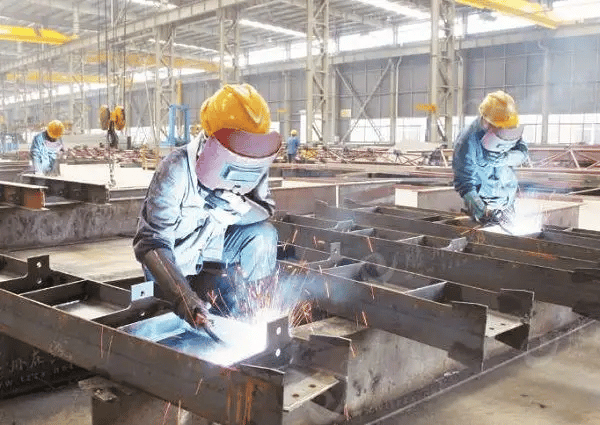
Condition and Requirements
Welders shall be qualified by training and obtain qualification certificates before they can undertake welding work.
For important welds of important structural parts, both ends of welds or the intersection of welds must be stamped with welder code.
Before welding, the welding parts should be cleaned of dirt near the surface of the weld, such as oxide scale, oil, anticorrosive paint, etc.
When welding below zero degrees Celsius, the following conditions should be observed:
- Ensure that the weld can freely shrink during welding;
- do not use a heavy hammer to hit the welded structural parts;
- Before welding, remove all the ice and snow on the welded structural parts;
- Before welding, preheat according to the provisions, the specific temperature is determined according to the process test.
Before welding should be preheated according to the provisions, must be sealed welding motherboard (web), rib plate, partition end (thickness direction) and the connector exposed end of the gap;
Concealed parts of steel structure should be welded, coated and sealed after passing inspection.
Double-sided butt welding should pick welding root, pick welding root can use a pneumatic shovel, carbon arc gouging, gouging and mechanical processing methods.
Multi-layer welding shall be welded continuously, and each layer of weld pass shall be cleaned and inspected in time after welding, and the defects shall be removed before welding.
In the welding process, use a flat welding position as far as possible.
During welding, shall not use the electrode with peeling or rusty welding core and the flux with damp agglomeration and the slag shell that has been melted; The welding wire and welding nail should be cleaned of oil and rust before use.
Further Reading: Steel Structure Installation & Design
The construction unit for the first use of steel, welding materials, welding methods, post-welding heat treatment, etc., shall carry out welding process evaluation, write a process evaluation report, and determine the welding process according to the evaluation report.
Welder stop welding time of more than 6 months, should be reassessed.
Welding, welders should comply with the welding process, not free welding and arc on the base metal outside the weld bead.
Butt joint, t-shaped joint, corner joint, cross joint butt weld and butt and corner joint combination weld, should be set at both ends of the welding arc and lead plate, the material and groove form should be the same as the weldment.
Length of arc initiation and lead weld: submerged arc welding should be greater than 50mm, manual arc welding and gas-shielded welding should be greater than 20mm. After welding, gas cutting should be used to cut off the arc and lead plate, and polished smooth, shall not be shot down with a hammer.
Weld cracks, welders shall not handle without authorization, should find out the cause, set out the repair process can be processed. The number of repairs of the same part of the weld should not exceed two times. When done more than two times, the repair process should be carried out according to the repair process.
After welding, the welder should clean the slag on the surface of the weld and the spatter on both sides, and check the appearance quality of the weld. After passing the inspection, the welder’s steel mark shall be made on the welding seam part specified in the process.
Carbon structural steel should be cooled to the ambient temperature in the weld, and low-alloy structural steel should be welded for 24 hours before weld inspection.
The PEB Steel Building
The Other Additional Attachments
Building FAQs
- How to Design Steel Building Components & Parts
- How Much Does a Steel Building Cost
- Pre-Construction Services
- What is a Steel Portal Framed Construction
- How to Read Structural Steel Drawings
Blogs Selected for You
- The Main Factors Affecting The Cost of Steel Structure Warehouse
- How Steel Buildings Help Reduce Environmental Impact
- How to Read Structural Steel Drawings
- Are Metal Buildings Cheaper Than Wood Buildings?
- Benefits of Metal Buildings For Agricultural Use
- Choosing the Right Location For Your Metal Building
- Making a Prefab Steel Church
- Passive Housing & Metal –Made for Each Other
- Uses for Metal Structures You May Not Have Known
- Why Do You Need a Prefabricated Home
- What Do You Need To Know Before Designing a Steel Structure Workshop?
- Why Should You Choose a Steel Frame Home Over a Wooden Frame Home
Contact Us >>
Have questions or need help? Before we start, you should know that almost all prefab steel buildings are customized.
Our engineering team will design it according to local wind speed, rain load, length*width*height, and other additional options. Or, we could follow your drawings. Please tell me your requirement, and we will do the rest!
Use the form to reach out and we will be in touch with you as quickly as possible.
About Author: K-HOME
K-home Steel Structure Co., Ltd covers an area of 120,000 square meters. We are engaged in the design, project budget, fabrication, and installation of PEB steel structures and sandwich panels with second-grade general contracting qualifications. Our products cover light steel structures, PEB buildings, low-cost prefab houses, container houses, C/Z steel, various models of color steel plate, PU sandwich panels, eps sandwich panels, rock wool sandwich panels, cold room panels, purification plates, and other construction materials.